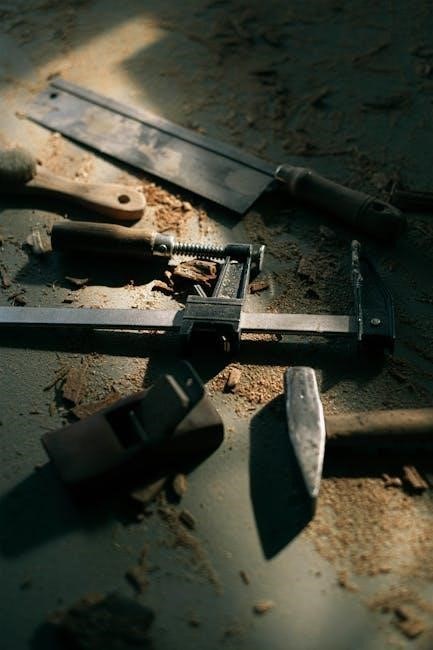
The Tag-Out Users Manual (TUM) provides critical safety protocols for isolating equipment and systems‚ ensuring personnel and ship safety while preventing improper operation and equipment damage.
1.1 Overview of the TUM
The TUM outlines procedures for safely isolating equipment and systems to prevent hazardous energy release. It covers danger tags‚ cautionary tags‚ and out-of-calibration labels‚ ensuring compliance with OSHA and NAVSEA standards. The manual emphasizes transitioning to electronic tag-out systems‚ with manual systems as an appendix for specific cases‚ providing a structured approach to tag-out processes for personnel safety and equipment protection.
1.2 Historical Background and Development
The Tag-Out Users Manual (TUM) was developed by NAVSEA to standardize safety protocols for isolating equipment and systems. Originating from naval safety requirements‚ the TUM evolved to meet OSHA standards and prevent hazardous energy incidents. Its development reflects advancements in tag-out practices‚ transitioning from manual systems to electronic programs for enhanced efficiency and compliance‚ ensuring personnel safety and equipment protection across naval operations.
Purpose and Scope of the Tag-Out Users Manual
The TUM provides safety protocols‚ isolates components‚ prevents improper operation‚ and transitions to electronic tag-out systems‚ ensuring compliance and efficiency across naval operations.
2.1 Primary Objectives of the TUM
The primary objectives of the Tag-Out Users Manual (TUM) are to ensure personnel and ship safety‚ prevent equipment damage‚ and avoid improper operation of isolated components or systems. It establishes standardized procedures for tag-out processes‚ ensuring compliance with safety regulations and effective control of hazardous energy sources across all naval systems and equipment.
2.2 Applicability Across Naval Systems and Equipment
The TUM applies to all naval systems‚ including shipboard components‚ equipment‚ and nuclear propulsion systems. It governs tag-out procedures for mechanical‚ electrical‚ and hydraulic systems‚ ensuring safety and operational integrity. The manual is mandatory for equipment tag-outs and instrument labels‚ applicable during maintenance‚ repair‚ and overhaul activities to prevent hazardous energy release and ensure compliance with safety standards.
Safety Protocols and Procedures
The TUM outlines essential safety measures to isolate equipment‚ prevent improper operation‚ and ensure personnel safety. It provides standardized procedures to safeguard against hazardous energy release.
3.1 Personnel and Equipment Safety Measures
The TUM emphasizes protocols to protect personnel and equipment‚ ensuring safe working conditions. Danger tags indicate immediate hazards‚ while cautionary tags provide special instructions. These measures prevent equipment damage and improper operation‚ aligning with OSHA and NAVSEA standards to safeguard both human and material resources effectively.
3.2 Prevention of Improper Equipment Operation
The TUM outlines clear procedures to prevent improper equipment operation‚ ensuring components are safely isolated. Danger tags and cautions are used to alert personnel of potential hazards‚ while specific isolation processes prevent accidental startups or unauthorized access‚ safeguarding both equipment and operators in compliance with OSHA and NAVSEA guidelines.
3.3 Isolation of Components and Systems
The TUM specifies methods for isolating components and systems to ensure safe maintenance. Proper tag-out procedures‚ including danger tags and cautions‚ are emphasized to prevent accidental activation. Isolation ensures equipment remains in a safe state‚ aligning with NAVSEA policies and OSHA standards to protect personnel and prevent equipment damage during maintenance operations.
Types of Tags and Labels
Danger tags (red) indicate isolation‚ cautionary tags (yellow) provide special instructions‚ and out-of-calibration labels (red) mark defective equipment‚ ensuring clear safety communication and compliance.
4.1 Danger Tags and Their Usage
Danger tags are red and indicate equipment isolation due to unsafe conditions. They prevent accidental operation‚ protecting personnel from hazardous energy. Usage is strictly regulated‚ ensuring compliance with NAVSEA and OSHA standards. These tags are essential for immediate visual alerts‚ emphasizing critical safety measures during maintenance or repair activities.
4.2 Cautionary Tags for Special Instructions
Cautinary tags‚ typically yellow‚ provide special instructions or indicate the need for extra care during equipment operation. They are used when equipment doesn’t pose an immediate danger but requires specific precautions. These tags complement danger tags‚ ensuring safe operations and compliance with NAVSEA and OSHA standards while maintaining clear communication for personnel involved in maintenance or repair activities.
4.3 Out-of-Calibration Labels
Out-of-calibration labels‚ typically red‚ indicate equipment is defective or isolated‚ preventing improper use. They alert personnel that the equipment requires recalibration before safe operation‚ ensuring accuracy and reliability. These labels are essential for maintaining equipment integrity and personnel safety‚ adhering to NAVSEA and OSHA standards for proper maintenance and operational procedures.
Electronic vs. Manual Tag-Out Systems
The TUM emphasizes transitioning to electronic tag-out programs as primary requirements‚ with manual systems moved to an appendix for limited use‚ ensuring enhanced efficiency and compliance.
5.1 Transition to Electronic Tag-Out Programs
The transition to electronic tag-out programs enhances safety and efficiency by providing real-time tracking and reducing errors. The TUM now designates electronic systems as primary‚ moving manual processes to an appendix for limited use. This shift streamlines procedures‚ ensuring compliance with modern standards while maintaining the integrity of safety protocols for personnel and equipment across naval operations and maintenance activities.
5.2 Manual Tag-Out Systems and Their Limitations
Manual tag-out systems rely on physical tags and procedural checks‚ but they are prone to human error and lack real-time tracking. Their use is now limited to situations where electronic systems are unavailable. While they provide a visible indicator of isolation‚ they are less efficient and more susceptible to tampering or loss compared to electronic alternatives‚ requiring strict oversight to ensure safety and compliance.
Compliance and Regulatory Standards
The TUM ensures adherence to OSHA lockout/tagout requirements and NAVSEA policies‚ providing standardized safety protocols to prevent equipment damage and ensure personnel safety during maintenance operations.
6.1 OSHA Lockout/Tagout Requirements
OSHA’s 29 CFR 1910.147 mandates specific protocols for controlling hazardous energy during equipment maintenance. The TUM aligns with these standards‚ requiring the use of approved lockout/tagout devices‚ employee training‚ and regular audits to ensure compliance and prevent energy-related accidents.
6.2 NAVSEA Policies and Enforcement
NAVSEA enforces strict policies for tag-out procedures across naval systems‚ emphasizing personnel and ship safety. The TUM revision transitions to electronic tag-out programs‚ with manual systems as an appendix. Applicable to all naval ships‚ including nuclear propulsion‚ policies ensure equipment tag-outs and labels meet safety standards. Enforcement requires audits and adherence to local instructions‚ with CSOOW/EOOW oversight for compliance.
Training and Qualifications
The TUM mandates specific training for personnel involved in tag-out processes‚ ensuring understanding of safety protocols and proper procedures. Training must be comprehensive and regular‚ with retraining required for proficiency maintenance.
7.1 Personnel Training Requirements
The TUM outlines that personnel must undergo comprehensive training to understand safety protocols and tag-out procedures. Training includes understanding danger tags‚ proper tag application‚ and recognizing out-of-calibration labels. Personnel must demonstrate proficiency in applying tags correctly and following isolation procedures. Retraining is required periodically and when new procedures or equipment are introduced to maintain proficiency and ensure compliance with safety standards.
7.2 Retraining and Proficiency Maintenance
Retraining is essential to maintain personnel proficiency in tag-out procedures. It is required when new equipment or procedures are introduced‚ ensuring compliance with safety standards. Periodic evaluations assess understanding and application of protocols‚ while updates address changes in regulations or practices. This continuous improvement ensures safe operations and adherence to OSHA and NAVSEA guidelines.
Procedures for Tag-Out Application and Removal
Proper application and removal of tags ensure equipment safety and compliance with protocols. Detailed steps are outlined to prevent improper operation and maintain operational integrity.
8.1 Step-by-Step Tag-Out Process
The process begins with proper authorization‚ followed by isolating components and applying tags. Each step ensures equipment safety‚ verifying de-energization and documenting actions. Removal requires similar rigor‚ confirming system readiness and adherence to protocols. This structured approach guarantees operational integrity and compliance with safety standards‚ preventing hazardous energy release.
8.2 Authorization and Supervision
Tag-out activities must be authorized by designated personnel‚ such as the CSOOW/EOOW‚ ensuring compliance with safety protocols. Supervisors oversee the process‚ verifying proper tag application and removal. Personnel must be trained and qualified‚ with documentation maintained for accountability. Regular audits ensure adherence to procedures‚ reinforcing a culture of safety and regulatory compliance throughout all operations.
Auditing and Continuous Improvement
Regular audits ensure compliance with TUM standards‚ identifying gaps for improvement. Updates to procedures and training materials are implemented to enhance safety and efficiency continuously;
9.1 Conducting Tag-Out Audits
Audits are conducted to ensure compliance with TUM standards‚ verifying proper tag-out procedures and equipment isolation. Inspections‚ interviews‚ and documentation reviews are used to identify gaps and non-compliance. Corrective actions are implemented to address findings‚ ensuring personnel safety and operational integrity. Audits also evaluate the effectiveness of training programs and adherence to regulatory requirements‚ promoting continuous improvement in tag-out practices across all systems.
9.2 Updating Procedures for Future Enhancements
Procedures are updated to reflect advancements in technology‚ regulatory changes‚ and lessons learned from audits. Electronic tag-out programs are prioritized‚ reducing reliance on manual systems. Enhancements include improved training materials‚ streamlined processes‚ and integration of feedback from personnel. Updates ensure alignment with OSHA standards and NAVSEA policies‚ fostering a culture of safety and operational efficiency across naval systems.