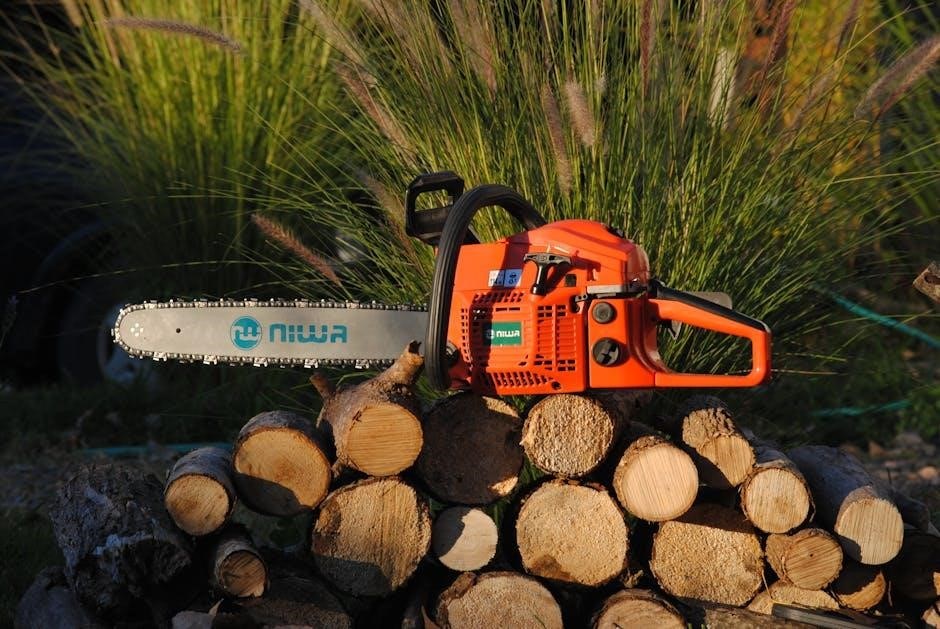
Choosing the right scroll saw blade is crucial for precise cuts and optimal performance․ This guide helps you select the perfect blade size for various materials and projects, ensuring smooth, accurate results every time․
Understanding the Importance of Blade Size
Blade size is critical for achieving precise cuts and optimal performance in scroll saw projects․ The right blade ensures smooth finishes, minimizes tear-out, and handles material thickness effectively․ Using an incorrect blade size can lead to poor results, increased vibration, or difficulty in cutting intricate details․ Blade size influences the tightness of turns, cut quality, and overall project success․ Selecting the appropriate blade size for your material and design is essential to avoid wasted time and materials․ This guide helps you understand how blade size impacts your work and how to choose the best blade for your specific needs․
Overview of Scroll Saw Blades
Scroll saw blades are available in various sizes and types, designed for different materials and cutting requirements․ They come in pinned and pinless configurations, with tooth configurations like skip, reverse, and standard teeth․ Blade sizes range from fine 2/0 blades for intricate details to larger, coarser blades for quicker cuts․ The choice of blade depends on factors like material thickness, desired finish, and project complexity․ Proper blade selection ensures efficient cutting, reduces wear, and enhances overall results․ Understanding blade types and their applications is key to mastering scroll saw projects and achieving professional-quality outcomes․
Factors Influencing Scroll Saw Blade Size
Blade size is influenced by material type, thickness, project complexity, and desired finish quality, ensuring optimal performance and precision in scroll saw projects․
Material Type and Thickness
Material type and thickness are critical factors in selecting the right scroll saw blade․ Hardwoods like maple or oak require thicker, sturdier blades, while softwoods may use thinner ones․ Non-wood materials, such as metal or plastic, demand specialized blades with unique tooth configurations․ Thicker materials need blades with higher rigidity to prevent breakage, while thinner materials can use more flexible blades for detailed cuts․ Understanding the specific characteristics of your material ensures proper blade selection, optimizing both performance and cutting accuracy․ This balance is essential for achieving professional-grade results in scroll saw projects․
Project Complexity and Detail Level
Project complexity and detail level significantly influence blade selection․ Intricate designs and tight curves require finer blades with higher TPI for precision․ Thicker blades are better suited for simpler, straighter cuts․ For fretwork and portraits, smaller blade sizes like 2/0 to 1 are ideal, allowing tight radius cuts with minimal tear-out․ Larger blades, however, excel in faster, rougher cuts․ Matching blade size to project complexity ensures smooth execution and prevents unnecessary blade stress, making the cutting process more efficient and the results more satisfactory․ This balance is key to mastering scroll saw craftsmanship․
Desired Finish Quality
Desired finish quality plays a vital role in blade selection․ For smooth, polished finishes, skip-tooth blades with higher TPI are recommended as they minimize tear-out and leave a cleaner edge․ Fine details and intricate cuts benefit from smaller blade sizes, which reduce material removal and prevent rough edges․ Conversely, projects requiring rapid cutting with less emphasis on finish can use larger, coarser blades․ Balancing blade characteristics with the desired finish ensures optimal results, whether creating fine art or functional pieces․ Proper blade choice enhances both efficiency and the final appearance of your scroll saw projects․
Understanding Scroll Saw Blade Specifications
Scroll saw blade specifications include blade length, width, teeth per inch (TPI), and tooth configuration․ These factors determine cutting accuracy, material compatibility, and finish quality, ensuring optimal performance for your projects․
Blade Length and Width
Blade length typically remains standard, while width varies to suit project needs․ Narrow blades, like 1/16 inch, are ideal for intricate cuts, while wider blades, up to 1/4 inch, handle straight lines and thicker materials․ The gullet size (space between teeth) affects chip clearance and cutting efficiency․ Wider blades provide stability but may limit maneuverability in tight curves․ Selecting the correct width ensures smooth cuts and prevents overheating, optimizing performance for your scroll saw projects․
Teeth Per Inch (TPI) and Tooth Configuration
Teeth Per Inch (TPI) determines the blade’s cutting aggressiveness and finish quality․ Lower TPI (e․g․, 10-14) is ideal for faster cuts in thicker materials, while higher TPI (e․g․, 20-28) suits intricate details and smoother finishes․ Tooth configuration, such as skip tooth or standard, affects chip clearance and cutting efficiency․ Skip tooth blades reduce dust and prevent clogging, making them suitable for soft materials․ Standard teeth are versatile for general woodworking․ Matching TPI and tooth type to your material ensures precise cuts and minimizes blade stress, optimizing performance for both intricate designs and heavy-duty projects․
Blade Thickness and Material Compatibility
Blade thickness is critical for stability and precision․ Thicker blades (0․035″ or more) are ideal for dense hardwoods and metals, offering rigidity and straighter cuts․ Thinner blades (0․020″-0․025″) excel in intricate fretwork and tight curves, reducing material loss․ Material compatibility varies; high-carbon steel blades are durable for woodworking, while bimetal blades are best for metal cutting․ Matching blade thickness to material type and thickness ensures smooth operation and prevents breakage․ Proper selection enhances both accuracy and tool longevity, making it a key factor in achieving professional-grade results in various scrolling projects․
Choosing the Right Blade for Your Material
Selecting the right blade ensures optimal performance for various materials․ From wood to metal, blade thickness and TPI significantly impact precision and finish quality․ This guide helps you choose wisely․
Blades for Hardwood and Softwood
For hardwood and softwood projects, blade selection depends on material thickness and desired finish․ Dense hardwoods like maple or oak require thicker blades, while less dense hardwoods like cherry may use slightly thinner options․ Softwoods generally allow for more flexibility in blade choice․ Blades with higher TPI (teeth per inch) are ideal for intricate cuts, while lower TPI blades are better for faster, rougher cuts․ Skip tooth blades are recommended for softwoods to minimize tearout and improve finish quality․ Always match blade size to material thickness for optimal performance and precision in your scroll saw work․
Blades for Metal and Non-Wood Materials
When cutting metal or non-wood materials, specialized blades are essential․ Blades numbered 3/0 to 5 are ideal for metals like copper, brass, and aluminum, handling thicknesses up to 1/8 inch․ These blades are designed with skip tooth configurations for efficient chip clearance and smoother cuts․ For tougher materials, higher TPI blades may be needed to maintain precision․ Always consider the material’s thickness and the project’s complexity to ensure the blade’s durability and performance․ Proper blade selection is key to achieving clean, accurate cuts in non-wood materials with minimal wear and tear on the blade․
Blades for Plastic and Composite Materials
For cutting plastic and composite materials, choose blades with a medium to high TPI for smooth finishes․ Skip tooth or standard tooth blades work well, depending on the material’s density․ Thinner blades are ideal for intricate cuts, while thicker blades provide stability for heavier composites․ Always match blade size to material thickness to avoid melting or warping; Proper blade selection ensures clean cuts and prevents damage to the material, making your projects look professional and polished․ Optimal blade choice is crucial for achieving precise results in plastic and composite materials․
Scroll Saw Blade Size for Specific Projects
Matching blade size to project-specific needs ensures precision and efficiency․ This section explores optimal blade choices for fretwork, portraits, and custom designs, enhancing your creative outcomes․
Fretwork and Intricate Designs
For intricate fretwork, smaller blades are essential․ Blades with a 2/0 to 1 size range are ideal, offering tight radius cuts and fine details․ Skip tooth configurations ensure smooth finishes and excellent chip clearance, reducing tear-out․ When working with materials like hardwood, softwood, or plywood, blade size should match material thickness․ For example, 1/4-inch thick materials benefit from a 2/0 blade, while thicker materials may require a slightly larger size․ Proper blade selection enhances precision and control, making complex designs achievable with minimal effort and optimal results․
Portraits and Fine Details
Portraits and fine details demand precision․ Blades in the 2/0 to 1 range are recommended, as they provide the necessary control for intricate cuts․ Skip tooth blades are ideal, offering smooth finishes with minimal tear-out․ For materials up to 1/4-inch thick, a 2/0 blade excels, while slightly thicker materials may require a 1․ Maintaining blade sharpness is crucial for clear, detailed cuts․ Proper blade size ensures sharp lines and accurate portrayals, making your scroll saw work stand out with exceptional clarity and professionalism․
Custom Designs and Patterns
Custom designs and patterns often require a balance between precision and flexibility․ Blades in the 3/0 to 5 range are versatile for intricate patterns, offering smooth cuts and good chip clearance․ For detailed custom work, skip tooth blades are recommended, as they minimize tear-out and provide a cleaner finish․ Thicker materials may need wider blades for stability, ensuring accurate cuts without wobbling․ Adjusting blade size based on design complexity and material thickness ensures optimal results, allowing you to achieve the desired intricate patterns and custom designs with precision and professionalism․
General Tips for Selecting Scroll Saw Blades
Selecting the right scroll saw blade involves balancing material thickness, project complexity, and desired finish․ Match blade size to your project’s requirements for optimal performance and precision․
Matching Blade Size to Project Requirements
Matching the blade size to your project ensures precise cuts and prevents damage․ For intricate designs, use smaller blades with higher TPI for detail without compromising material integrity․ Thicker materials require sturdier blades to maintain stability and avoid breakage․ Consider the type of material—wood, metal, or plastic—and its thickness when selecting․ A smaller blade number means tighter turns, ideal for fretwork, while larger blades are better for straight cuts․ Always refer to a blade chart to cross-reference material thickness and project complexity for the best results․ Proper blade selection enhances both efficiency and the quality of your finished work․
Blade Maintenance and Optimization
Proper blade maintenance is essential for optimal performance and longevity․ Regularly clean blades to remove debris and resin buildup, ensuring smooth cuts․ Lubricate blades during cuts to reduce friction and heat, especially when working with metals․ Store blades in a dry place to prevent rust․ Inspect blades for damaged or dull teeth and replace them promptly․ Avoid over-tightening, as this can cause premature breakage․ For intricate cuts, consider using skip-tooth blades for better chip clearance․ Proper blade care enhances accuracy, reduces wear, and ensures consistent results across all your scroll saw projects․ Regular maintenance also prolongs blade life and improves overall efficiency․
Troubleshooting Common Blade Issues
Common blade issues include breakage, poor finish quality, and inaccurate cuts; Blade breakage often results from improper tension, excessive speed, or using the wrong blade for the material․ To fix, ensure proper tension and match blade size to material thickness․ For poor finish quality, check for dull blades or incorrect Teeth Per Inch (TPI)․ Swap blades if necessary and adjust cutting speed․ Inaccurate cuts may stem from misaligned blades or incorrect setup․ Verify blade alignment and ensure the material is securely clamped․ Regular blade maintenance, such as cleaning and lubricating, can prevent many issues․ Addressing these problems ensures smoother, more precise cutting results․
Blade Size-Speed Chart for Optimal Performance
Matching blade size to speed ensures optimal performance․ Most blades operate between 800-1200 SPM; smaller blades require lower speeds to prevent breakage․ Proper pairing enhances accuracy and extends blade life․
Recommended Speeds for Different Blade Sizes
Blade size and speed are closely linked for optimal performance․ Smaller blades, like 2/0, typically run at 800-1100 SPM for intricate cuts, while larger blades (e․g․, size 5) can handle up to 1200 SPM․ Increasing speed enhances cutting efficiency but risks blade breakage and heat buildup․ For materials like metals, slower speeds are recommended to maintain control and prevent damage․ Adjusting speed based on blade size ensures smoother cuts, reduces tear-out, and prolongs blade life․ Proper pairing of blade size and speed is essential for achieving desired results in various materials and project complexities․
Adjusting Speed for Material Thickness
Material thickness plays a key role in determining the optimal scroll saw speed․ Thinner materials, such as 1/8″ wood or metal, require slower speeds to prevent breakage, while thicker materials can handle higher speeds․ For example, blades sized 2/0 to 5 are often used for materials up to 1/4″ thick, operating between 800-1200 SPM․ Thicker materials, like 1/2″ metal, may need larger blades (size 7 or higher) at slightly higher speeds, but exceeding 1200 SPM can cause blade overheating․ Balancing speed with material thickness ensures clean cuts and extends blade longevity, especially for intricate or detailed work․
Selecting the right scroll saw blade size is crucial for precise cuts and material compatibility․ Proper blade size and speed adjustments ensure optimal performance, preventing overheating and extending blade life․ Always refer to detailed charts and guides for specific material thicknesses and project requirements to achieve professional results and maintain tool longevity․
Final Thoughts on Blade Selection
Selecting the right scroll saw blade is essential for achieving precise cuts and optimal performance․ By considering material type, thickness, and project complexity, you can choose the ideal blade․ fine details require smaller blades with higher TPI, while thicker materials need larger, sturdier blades․ Always maintain your blades and use the recommended speeds to prevent overheating and extend their lifespan․ Experimenting with different blades and techniques will enhance your skills, ensuring professional-quality results․ Keep a blade chart handy for quick reference, and remember, the right blade makes all the difference in your scroll saw projects․
Resources for Further Reading
For deeper insights, explore official manufacturer guides like Olson’s or Bearwood’s technical manuals․ Websites specializing in woodworking tools often offer detailed blade charts․ The “Never Fail Blade Chart” is a valuable resource, cross-referencing materials and blade types․ Woodworking forums and communities share practical tips from experienced craftsmen․ Additionally, instructional videos on platforms like YouTube provide visual guidance․ These resources help refine blade selection skills, ensuring optimal performance for any scroll saw project․ Always consult reputable sources to stay updated on the latest blade technologies and techniques․